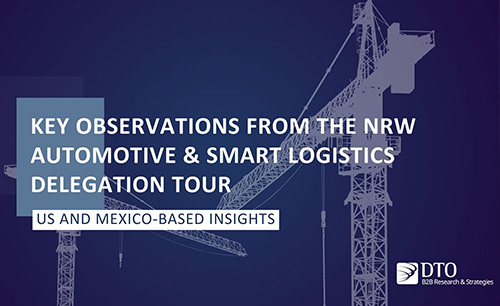
Key Observations from the NRW Automotive & Smart Logistics Delegation Tour
Our US managing director, Sophia Dietsch, partook in a delegation tour across Nashville and Monterrey Mexico last year which provided a first-hand look into the evolving challenges and opportunities within the automotive and logistics sectors. Here are some of the most pressing
1. Workforce Challenges: The Talent Gap & Skill Development
A recurring theme across the manufacturing plants visited was the difficulty in attracting, training, and retaining skilled labor. Several factors contribute to this issue:
- Aging Workforce: Many skilled professionals are nearing retirement, leaving a gap that younger workers are hesitant to fill, particularly in specialized manufacturing roles.
- Talent Competition: Manufacturers are competing with other industries, such as tech and logistics, for the same skilled workforce, driving wages up and making hiring more challenging.
- Vocational Training Needs: Companies are addressing this by investing in apprenticeship programs, partnerships with local technical schools, and on-site training centers to equip workers with the necessary skills.
In Mexico, manufacturers are leveraging a younger workforce (average age ~29 years) and developing localized training programs to enhance skill development.
2. Energy Supply & Sustainability: Striving for Efficiency and Renewables
The energy crisis and sustainability concerns were top of mind for German manufacturers & suppliers in both the U.S. and Mexico. Some key energy-related challenges include:
- Rising Energy Costs: Electricity prices, particularly in Mexico, have fluctuated, prompting companies to seek alternative power solutions to maintain cost efficiency.
- Renewable Energy Integration: Several manufacturers are actively investing in solar, wind, and hydro energy sources to reduce reliance on fossil fuels and enhance long-term sustainability.
- Carbon Footprint Reduction: Companies are implementing energy-efficient processes, such as LED lighting, heat recovery systems, and smart automation, to lower emissions and meet sustainability targets.
In Mexico, the regulatory framework governing self-generated electricity, particularly from renewable sources like solar, has undergone significant changes, leading to complexities for companies aiming to utilize their own generated power for manufacturing. While Mexico has significant potential for renewable energy, the evolving regulatory environment presents challenges for companies aiming to utilize self-generated power for manufacturing. Businesses must navigate these complexities carefully, ensuring compliance with current laws and regulations, and stay informed about ongoing policy developments to effectively manage their energy strategies.
Recent Developments:
In recent years, the Mexican Energy Regulatory Commission (CRE) has taken actions against companies operating under the self-supply model. For instance, in 2022, the CRE imposed significant sanctions on firms deemed to be violating the terms of their permits by effectively selling electricity to third parties, which is outside the scope of self-supply.
Implications for Companies:
These regulatory changes have created uncertainty for companies seeking to generate their own power. While small-scale distributed generation projects (e.g., rooftop solar installations producing under 0.5 MW) have seen growth, larger-scale projects face regulatory hurdles. The government has emphasized strengthening the CFE and has set new rules for private electricity producers, including clean energy generators. Private producers are now allowed to generate up to 9.55 gigawatts of renewable electricity by 2030, provided they comply with the requirements of safety and reliability of the national grid.
3. Supply Chain Resilience: Adapting to Global Disruptions
The global supply chain remains fragile, and manufacturers are still feeling the effects of past disruptions. The biggest concerns include:
- Nearshoring Trends: The automotive sector is shifting toward nearshoring strategies, where manufacturers move production closer to end markets to mitigate supply chain risks. This trend is especially evident in Mexico, where companies benefit from free trade agreements (FTAs) and proximity to the U.S. market. The rise of new tariffs on Mexican imports could now accelerate reshoring efforts in the U.S., as companies reassess their supply chain dependencies and consider alternative production hubs.
- Supplier Diversification: Companies are reducing reliance on single suppliers and building redundancy into their supply chains to avoid production halts caused by component shortages.
- Logistics Optimization: Manufacturers are utilizing real-time tracking, AI-driven inventory management, and predictive analytics to streamline logistics and ensure smoother operations.
4. Trade Policy & Market Uncertainty: The Impact of Tariffs & Regulations
Manufacturers are closely monitoring policy changes, particularly the impact of U.S. tariffs on Mexican imports. The implications include:
- Increased Costs: Tariffs could raise production costs, forcing companies to either absorb losses or pass costs onto consumers.
- Shift in Investment Strategy: Some companies are re-evaluating where they place future investments. If tariffs persist, there could be a shift toward U.S.-based production or alternative sourcing.
The automotive sector is already a highly globalized industry, and these new trade barriers could disrupt established manufacturing ecosystems in North America.
Conclusion: What’s Next for the Industry?
The insights from this delegation highlight the resilience and adaptability of manufacturers in both the U.S. and Mexico. Companies are actively investing in:
✔ Skilled labor programs to mitigate workforce shortages
✔ Sustainable energy solutions to reduce operational costs and meet regulatory expectations
✔ Robust supply chain strategies to navigate global disruptions
✔ Smart manufacturing technologies to drive efficiency and competitiveness
As trade policies continue to evolve, manufacturers must remain agile, data-driven, and proactive to sustain growth in an increasingly complex global environment.